Why Testing Controlled Environments Is Critical for Your Business
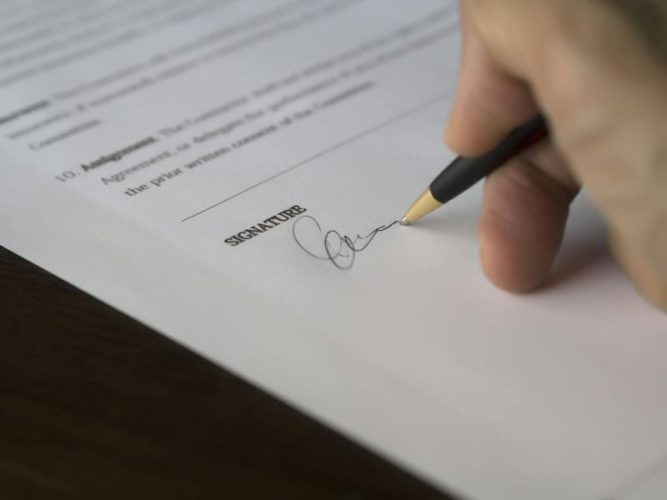
Categories :
Professionals who test and certify controlled environments play a crucial role in ensuring the safety, efficiency, and compliance of various industries. These experts are equipped with specialized knowledge and tools to assess conditions such as temperature, humidity, air quality, and contamination levels. By rigorously evaluating controlled environments, whether in laboratories, manufacturing facilities, or healthcare settings, they help maintain optimal conditions that meet regulatory standards and industry best practices. Their meticulous work not only safeguards human health and product integrity but also enhances operational performance and minimizes risks.
Ensuring Compliance with Regulatory Standards
Adhering to regulatory standards is paramount for businesses operating in controlled environments. Failing to comply can lead to severe penalties, product recalls, and damage to a company's reputation. Regulatory bodies such as the FDA, EPA, and ISO establish stringent guidelines that must be met to ensure the safety and efficacy of products and processes.
Professionals who test controlled environments are well-versed in these regulations. They use their expertise to perform comprehensive evaluations and generate detailed reports that demonstrate compliance. This documentation is critical during audits and inspections, providing evidence that the controlled environment meets or exceeds required standards.
Maintaining compliance is not a one-time task but an ongoing responsibility. Continual monitoring and periodic testing are essential to identify and address any deviations from regulatory requirements, thereby ensuring sustained compliance and operational excellence. The folks at Keystone CT note that regular testing also helps to identify potential issues and implement corrective actions before they escalate into major problems. It is a proactive approach that can save businesses time, money, and resources in the long run.
Mitigating Contamination Risks
Contamination control is a significant concern in controlled environments, particularly in industries such as pharmaceuticals, biotechnology, and healthcare. Even the slightest contamination can compromise product integrity, leading to costly recalls and potential harm to consumers or patients.
Testing professionals implement stringent protocols to detect and mitigate contamination risks. They assess factors such as air particulate levels, microbial presence, and surface cleanliness to ensure that the environment remains within acceptable contamination thresholds. Advanced technologies, such as particle counters and microbial samplers, enable precise detection and measurement.
By identifying sources of contamination and implementing corrective actions, businesses can prevent costly disruptions and ensure that their products maintain high quality. This proactive approach not only protects consumers but also bolsters a company’s reputation for safety and reliability.
Optimizing Operational Efficiency
Controlled environments play a pivotal role in optimizing operational efficiency. By maintaining precise environmental conditions, businesses can enhance the performance and longevity of their equipment and processes. For example, in a manufacturing facility, consistent temperature and humidity levels can prevent equipment malfunctions and product defects.
Professionals conducting environmental testing assess factors like airflow patterns, temperature uniformity, and humidity control to identify areas for improvement. Through their evaluations, businesses can make informed adjustments to their HVAC systems and other environmental controls, resulting in more efficient operations.
Optimizing operational efficiency often translates to cost savings. Efficiently managed controlled environments reduce energy consumption, minimize waste, and prolong the life of expensive equipment, ultimately boosting profitability and sustainability.
Enhancing Product Quality
High product quality is a cornerstone of business success, and controlled environments are critical in achieving this standard. Environmental conditions directly impact the quality and consistency of products, particularly in sectors like pharmaceuticals, food production, and electronics.
Environmental testing professionals ensure that conditions such as temperature, humidity, and air quality are meticulously controlled to meet the stringent requirements of the production process. By doing so, they help businesses maintain high product quality and avoid costly production issues.
Controlled environments also facilitate the research and development of new products. Accurate control of environmental variables allows for more reliable testing and experimentation, leading to innovative and high-quality product offerings.
Safeguarding Health and Safety
The health and safety of employees and consumers are paramount, especially in environments where hazardous materials or sensitive processes are involved. Controlled environments are designed to mitigate health and safety risks by maintaining optimal conditions that prevent exposure to harmful substances.
Testing and certification professionals play a critical role in safeguarding health and safety. They assess potential risks, such as chemical exposure, airborne contaminants, and equipment hazards, implementing measures to address these concerns. Regular testing ensures that all protective systems, such as air filtration and containment units, function correctly.
By maintaining a safe controlled environment, businesses can protect their workforce, comply with occupational health and safety regulations, and reduce the likelihood of workplace incidents. This not only fosters a safer working environment but also enhances employee morale and productivity.
Boosting Customer Confidence
Customer confidence is an integral aspect of a successful business, especially in industries reliant on strict environmental controls. When customers are assured that products are manufactured, stored, and handled under optimal conditions, it bolsters their trust and loyalty. Certified controlled environments serve as a testament to a company's commitment to quality and safety, offering a competitive advantage in the market.
Detailed environmental testing reports play a crucial role in transparency, allowing customers to see the rigorous measures taken to ensure product excellence. This transparency not only elevates trust but also enhances the company's reputation. Customers who receive consistently high-quality products are more likely to remain loyal and recommend the company's offerings to others, driving business growth through positive word-of-mouth.
Meeting and exceeding industry standards positions businesses as leaders in their field, further boosting customer confidence. Regularly demonstrating compliance with regulations and proactive contamination control strategies underscores a company’s dedication to maintaining the highest standards. Ultimately, this fosters a robust customer base that values reliability and excellence in every purchase. It is clear that testing and certifying controlled environments are critical components of a successful business.
The critical role of testing controlled environments cannot be understated. From ensuring compliance with regulations to mitigating contamination risks and enhancing operational efficiency, these professionals are integral in driving business success. By prioritizing environmental testing and certification, businesses can safeguard their operations, protect their employees and customers, and establish themselves as leaders in their industry. When it comes to controlled environments, thorough testing is critical for every business. Companies should partner with experienced professionals and make environmental testing an integral part of their operations to ensure continued success and growth.
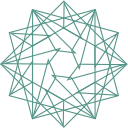
Citiesabc was created by a team of global industry leaders, academics and experts to create new solutions, resources, rankings and connections for the world’s top cities and populations.