The Science Behind Hydrogen Sensors: Detecting the Invisible Threat
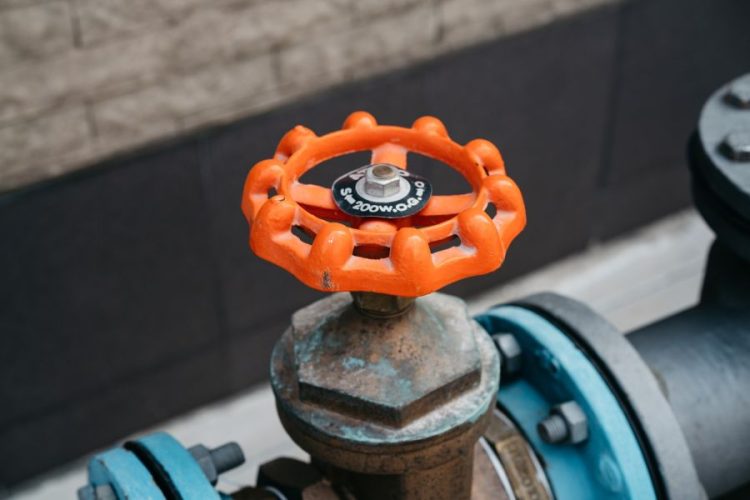
Categories :
Hydrogen is a powerful, sustainable energy source with immense potential, but it comes with a hidden danger: its invisibility. Colorless, odorless, and highly flammable, hydrogen can be hazardous when it leaks into the environment. The solution? Advanced hydrogen sensors. These sensors are essential in detecting hydrogen leaks, ensuring safety across industries. Here’s a closer look at how they work and why they're vital for safety.
Sensor Placement: Maximizing Safety and Efficiency
The placement of hydrogen sensors is as crucial as their accuracy. Sensors are typically installed in areas where hydrogen is stored, transferred, or used in production processes. Since hydrogen is lighter than air, sensors should be positioned at higher levels where hydrogen gas is most likely to accumulate. To maximize safety and efficiency, industrial hydrogen sensing can provide real-time monitoring and rapid detection to prevent leaks from reaching hazardous levels. Proper placement ensures rapid detection and optimizes sensor efficiency, reducing potential hazards in both small-scale and large-scale operations.
Understanding the Risks of Hydrogen Leaks
Hydrogen gas has a low ignition energy, which means it can ignite with a simple spark, and it burns at a temperature that is nearly invisible to the human eye. Since hydrogen is both colorless and odorless, detecting it without sensors is virtually impossible. This makes it critical to employ precise, reliable detection systems, especially in industries like transportation, manufacturing, and energy, where hydrogen use is expanding.
How Hydrogen Sensors Work
Hydrogen sensors are designed to detect and measure hydrogen concentration in the air, immediately alerting operators to the presence of this potentially dangerous gas. There are several types of hydrogen sensors, each operating on different scientific principles, including electrochemical, catalytic, and thermal conductivity. These sensors interpret chemical and thermal changes that occur when hydrogen is present, providing real-time detection and enabling quick action.
- Electrochemical Detection: Electrochemical hydrogen sensors detect hydrogen by using a chemical reaction that produces an electric current. When hydrogen enters the sensor, it interacts with electrodes and generates an electrical signal proportional to the hydrogen concentration. These sensors are highly sensitive and are particularly suited for low-power applications, making them ideal for environments where precise, constant monitoring is needed.
- Catalytic Combustion: Catalytic bead sensors detect hydrogen through combustion on a catalytically active bead. When hydrogen and oxygen meet on this heated surface, the reaction generates heat, increasing the bead’s temperature and changing its electrical resistance. The sensor monitors these resistance changes, providing a reliable measure of hydrogen concentration, especially in industrial settings where the gas is present in larger volumes.
- Thermal Conductivity: Thermal conductivity sensors operate by measuring the thermal conductivity of the gas mixture. Hydrogen’s thermal conductivity is significantly higher than that of air, so even small hydrogen concentrations cause detectable changes. This type of sensor is particularly useful for continuous monitoring, as it provides stability over long periods and is less affected by environmental factors, making it a common choice in controlled industrial environments.
Electrochemical Hydrogen Sensors
Electrochemical sensors are popular for hydrogen detection because of their accuracy and sensitivity. These sensors operate through a chemical reaction that generates an electrical signal proportional to the concentration of hydrogen present. As hydrogen enters the sensor, it reacts at the electrode surface, producing a current that is measured and reported. This type of sensor is ideal for environments that demand highly accurate readings and minimal power consumption.
Catalytic Bead Sensors: Simple Yet Effective
Catalytic bead sensors are another common solution for hydrogen detection. These sensors rely on a reaction between hydrogen and oxygen on a heated bead coated with a catalyst. When hydrogen is present, it combusts on the bead, causing a temperature change that alters the bead’s electrical resistance. The sensor measures this resistance change and calculates the hydrogen concentration. Though simple, catalytic bead sensors are effective, making them widely used in industrial settings.
Thermal Conductivity Sensors for Continuous Monitoring
Thermal conductivity sensors are frequently used in hydrogen detection due to their stability and durability. These sensors measure the thermal conductivity of gases, which change when hydrogen is present. As hydrogen has a much higher thermal conductivity than air, even a small concentration can produce a noticeable change in the sensor’s reading. This makes thermal conductivity sensors suitable for continuous monitoring in settings where hydrogen use is constant.
- High Sensitivity: One of the primary benefits of thermal conductivity sensors is their ability to detect very low concentrations of hydrogen. This high sensitivity is crucial for safety, as it allows for the early detection of leaks before they become hazardous. By identifying even minimal levels of hydrogen, these sensors can trigger alarms and prompt immediate action, significantly reducing the risk of explosions or other dangerous incidents.
- Robust Design: Thermal conductivity sensors are designed to withstand harsh industrial environments, making them ideal for continuous monitoring applications. They can function effectively in a wide range of temperatures and pressures, ensuring reliable performance in various conditions. This robustness means that facilities can deploy these sensors in locations with high vibration, humidity, or temperature fluctuations without worrying about performance degradation.
- Real-Time Monitoring: These sensors provide real-time data on hydrogen concentrations, which is essential for maintaining safety standards in environments where hydrogen is present. The ability to continuously monitor gas levels means that operators can respond swiftly to any changes, reducing the time it takes to address potential leaks.
The Importance of Sensitivity and Speed in Hydrogen Detection
A key feature of hydrogen sensors is their ability to quickly detect low levels of hydrogen to prevent accumulation and reduce the risk of explosion. High sensitivity ensures that even minimal leaks are detected before reaching dangerous concentrations. Quick response times are essential for alerting personnel in real time, enabling them to take corrective measures before hydrogen levels reach a critical threshold.
The Role of Calibration and Maintenance
Calibration and regular maintenance are essential for keeping hydrogen sensors accurate and reliable. Calibration aligns the sensor's readings with known hydrogen concentration levels, ensuring its output remains correct over time. Regular maintenance checks are necessary to prevent degradation or contamination, which could impair sensitivity or lead to false readings. A well-maintained sensor is your first line of defense in hydrogen safety.
Future Innovations in Hydrogen Detection Technology
With hydrogen’s growing role in energy and industry, hydrogen sensor technology is rapidly advancing. Emerging sensor designs are focusing on even greater sensitivity, longer battery life, and integration with smart monitoring systems. In the future, you may see hydrogen sensors connected to automated systems that can instantly cut off hydrogen supplies or activate alarms, offering an additional layer of safety.
Hydrogen sensors are essential for detecting the invisible threat posed by hydrogen gas. By understanding the types of sensors available and their operating principles, you can make informed decisions to protect your environment from potential hydrogen-related hazards. Regular maintenance, proper sensor placement, and awareness of emerging technologies are key to creating a safer workspace in the age of hydrogen energy.
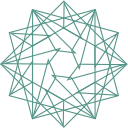
Citiesabc was created by a team of global industry leaders, academics and experts to create new solutions, resources, rankings and connections for the world’s top cities and populations.