The Importance of Proper Climate Control in Warehouses
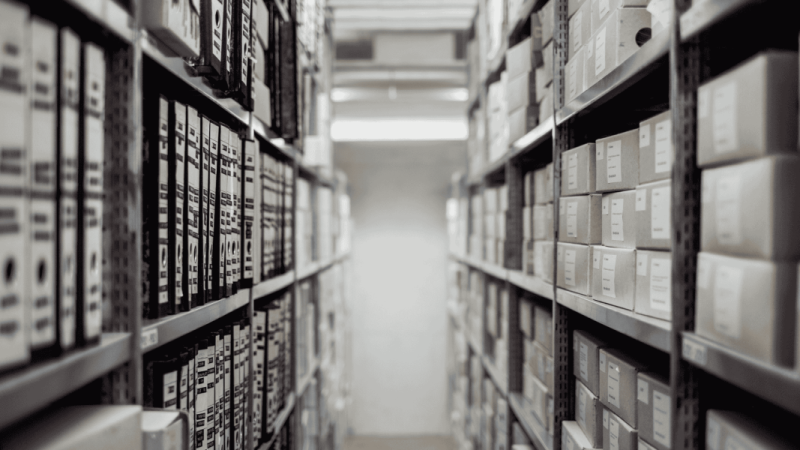
Categories :
Proper climate control in warehouses should be a top priority for any business that relies on stored goods. The effectiveness of climate control systems plays a pivotal role in safeguarding inventory, maintaining operational efficiency, and enhancing worker comfort. In particular, temperature, humidity, and air circulation must be adequately managed. Failure to do so can lead to spoilage, damage, and increased costs. Moreover, optimal climate control ensures compliance with regulatory standards across various industries.
Understanding the Basics of Climate Control
To appreciate the significance of climate control in warehouses, one must first understand its fundamental components. Effective climate control systems comprise heating, ventilation, and air conditioning (HVAC) units, which maintain consistent temperatures and reduce humidity levels. Proper temperature is crucial for many products, particularly perishable goods, chemicals, and electronics. If the temperature fluctuates beyond acceptable limits, it can damage products and compromise safety, leading to potential loss and liability. Humidity control is another crucial factor, especially for items susceptible to mold, rot, or rust.
Employing robust climate control systems helps mitigate these risks and maintains an environment conducive to inventory longevity. To achieve this, businesses increasingly seek specialized service providers, including local HVAC rentals. According to the reputable HVAC rental providers behind Total Construction Rentals, tailored equipment that meets specific environmental needs is beneficial here. Temporary portable heaters, air conditioners, and desiccant dehumidifiers can maintain industrial and commercial facilities' safety, comfort, and optimal climate.
The Impact of Poor Climate Control
Inadequate climate control can have severe repercussions for businesses. When temperatures and humidity are not adequately regulated, perishable goods can deteriorate, affecting quality and safety. For instance, food items stored in warehouses without adequate climate control can spoil rapidly, leading to significant financial losses. Furthermore, electronics stored in humid conditions risk corrosion and failure, triggering costly replacement expenses. Prolonged exposure to unsuitable conditions may also accelerate wear and tear on the warehouse infrastructure itself. It can foster the growth of mold and mildew, potentially making the workspace unhealthy for employees. These disadvantages highlight the importance of vigilant climate management and the potential costs of neglecting this crucial aspect.
Benefits of Proper Climate Control
Implementing effective climate control systems offers several benefits for warehouse operations. One primary advantage is preserving inventory quality, which translates to long-term cost savings and customer satisfaction. Proper regulation helps adhere to safety and regulatory standards, avoiding penalties and aligning operations with best practices. Additionally, efficient climate control contributes to productivity, as employees work better in a comfortable environment. Studies show that employees perform tasks more efficiently and accurately when not subjected to extreme temperatures or humidity. Moreover, businesses can project a positive image by maintaining an organized and climate-controlled warehouse, instilling confidence in clients and partners.
Choosing the Right Climate Control System
Selecting the appropriate climate control system requires thorough analysis and planning. Businesses must consider their specific needs concerning inventory volatility, warehouse layout, and local weather conditions. Consulting with HVAC professionals can aid in identifying suitable systems designed to meet unique specifications. Additionally, regular maintenance of climate control systems is vital in ensuring longevity and efficiency. Many businesses opt for local HVAC rentals instead of investing heavily in permanent installations. This approach allows them to obtain high-quality equipment without the upfront costs associated with purchase. For example, companies can engage services from reputable providers, ensuring their climate control needs are met economically.
Energy Efficiency and Cost Management
Energy efficiency is a crucial consideration for businesses managing warehouse climate control systems. Poorly managed systems can lead to excessive energy bills, impacting overall operational budgets. In recent years, there has been a significant push for innovative solutions to enhance energy efficiency within warehouses. Enhanced systems integrate innovative technology, allowing businesses to monitor and manage climate controls remotely. These developments not only reduce energy consumption but also lower operational costs. Many local HVAC rentals offer energy-efficient models, decreasing the ecological footprint and ensuring compliance with environmental regulations. By investing in these advanced systems, businesses can achieve sustainability and cost savings, reinforcing their commitment to responsible operations.
The Role of Technology in Climate Control
The advancement of technology has transformed how businesses today manage climate control in warehouses. Automation has introduced smart thermostats and monitoring systems capable of adjusting the environment based on real-time data. This technology provides significant benefits, such as reduced energy consumption and improved regulation of atmosphere variables. Business owners can benefit from software tools that provide analytics regarding climate patterns, enabling proactive adjustments to optimize conditions. Additionally, integrating Internet of Things (IoT) devices can help ensure that the climate control systems operate efficiently, providing alerts when parameters fall outside the set ranges. As technology evolves, businesses must stay informed and leverage these advancements to improve operational efficiency and maintain a competitive edge.
Proper climate control in warehouses significantly impacts inventory quality, employee efficiency, and overall operational excellence. Understanding climate control elements allows businesses to choose suitable systems based on their needs. Companies should consider local HVAC rentals for tailored solutions, enhancing the ability to adapt to changing requirements and maintaining an optimal environment. Likewise, embracing advanced technologies can drive efficiency and foster resilience in an ever-evolving industry. Mastering climate control in warehouse settings is essential for product preservation and a crucial component of good business practices.
Read More:
top 5 worst cities in new york
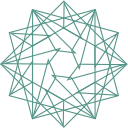
Citiesabc was created by a team of global industry leaders, academics and experts to create new solutions, resources, rankings and connections for the world’s top cities and populations.