The Impact of Injection Molding on Modern Manufacturing Processes
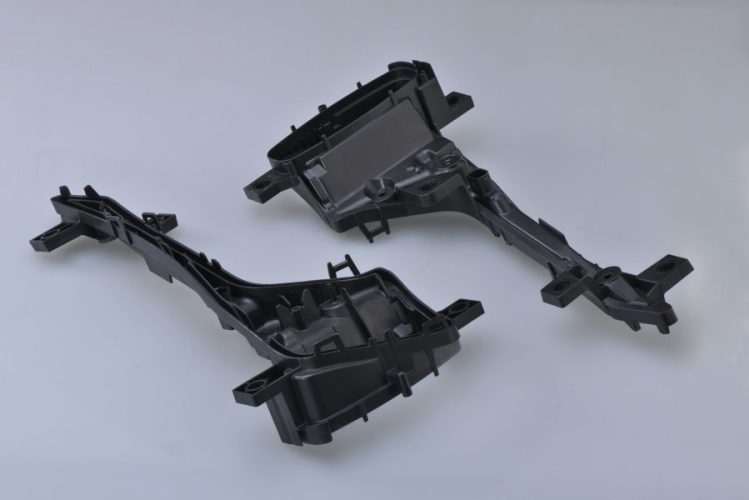
Categories :
Injection molding has emerged as one of the most influential manufacturing processes in the modern industrial landscape. As a technique that allows for the efficient production of complex parts with high precision, it has transformed how various products are manufactured, from consumer goods to intricate automotive components. This article delves into the significant impact of injection molding on manufacturing processes, exploring its advantages, applications, and innovations that shape the future of production.
A Brief Overview of Injection Molding
Injection molding operates by injecting molten material, typically plastic, into a mold, where it cools and solidifies into the desired shape. This method is renowned for its ability to create intricate designs while maintaining tight tolerances, which is crucial for many modern applications. The process is suitable for a wide range of materials, including thermoplastics, metals, and even certain types of ceramics, making it versatile for different manufacturing needs. The origins of injection molding date back to the 19th century, but its evolution over the past few decades has led to a significant enhancement in speed and efficiency. Automated systems and computer-aided design (CAD) technologies have further refined the process, paving the way for mass production with minimal human intervention. As industries strive for higher efficiency and lower costs, injection molding has become a cornerstone of modern manufacturing.
Advantages of Injection Molding
The advantages offered by injection molding are multi-faceted, making it an appealing choice for manufacturers across various sectors. One key benefit is its ability to produce high volumes of parts with consistent quality. Once the mold is created, the subsequent production runs can yield thousands or even millions of identical pieces, drastically reducing per-unit costs. This scalability is essential in industries like automotive and consumer electronics, where mass production is the norm. Another significant advantage is the material efficiency inherent in injection molding. Also, waste is minimized since the process often requires only the exact amount of material needed for each part. Furthermore, many feed materials can be reprocessed and reused, contributing to more sustainable manufacturing practices. With the growing emphasis on eco-friendly solutions, injection molding aligns well with current trends toward reducing environmental impact.
Apart from cost-efficiency and sustainability, injection molding also allows for exceptional design flexibility. Manufacturers can create complex geometries that would be difficult or costly to achieve using traditional machining methods. This capability enables designers to innovate without sacrificing functionality, opening new doors for product development. To fully maximize the advantages of injection molding, collaboration among industries and injection molding experts at https://www.aimprocessing.com/en/small-part-injection-molding will be essential. These experts can provide insights into optimizing designs and processes, ensuring that manufacturers achieve the highest standards of efficiency and quality.
Applications Across Industries
The application of injection molding spans a wide array of industries, showcasing its versatility. In the automotive sector, it is employed to create dashboard components, exterior panels, and numerous other parts that require both durability and aesthetic appeal. The precise nature of injection molding ensures that parts fit together seamlessly, meeting the stringent safety standards that define the industry. In consumer electronics, injection molding can be seen in action through housings for smartphones, tablets, and various gadgets. The process enables the production of lightweight yet robust enclosures tailored to accommodate the latest technology advancements while allowing for sleek designs. As technology continues to evolve, the demand for high-performance parts produced via injection molding is set to increase. Medical devices have also significantly benefited from injection molding technologies. The healthcare sector requires stringent quality and safety regulations, and the ability to produce high-precision components is invaluable. Items such as syringes, surgical tools, and implantable devices are meticulously crafted using advanced injection molding techniques, proving the method’s critical role in medical advancements.
Technological Innovations in Injection Molding
As industries advance, so does injection molding technology. Recent innovations have further enhanced the efficiency, precision, and environmental sustainability of the injection molding process. The integration of advancements such as smart sensors and artificial intelligence (AI) in machinery has led to greater automation and predictive maintenance capabilities. These smart technologies allow manufacturers to monitor the molding process in real-time, identifying potential issues before they escalate into larger problems. Such proactive measures are critical in maintaining production timelines, ensuring quality standards, and minimizing downtime. The use of AI can also optimize mold design and manufacturer workflows, enhancing productivity and reducing costs associated with trial-and-error methods in design. New materials continue to emerge that can complement injection molding processes, expanding the range of applications. Biodegradable plastics, for example, are increasingly being studied and integrated, offering an environmentally friendly alternative to traditional materials. As sustainability becomes a priority for consumers, manufacturers are compelled to explore these innovative options.
The Future of Injection Molding
The future of injection molding appears promising, bolstered by ongoing advancements in technology and materials science. As global manufacturing trends lean towards customization and rapid prototyping, injection molding stands to gain significantly. The methods employed today are adapting to meet the demands of industries seeking shorter lead times and personalized products. Emerging markets and the globalization of manufacturing are also expected to shape the future of this process. As new regions develop their manufacturing capabilities, injection molding could aid in local production, reducing lead times and transportation costs significantly. Additionally, as industries become more interconnected, there is potential for innovation to be shared across borders, pushing the boundaries of what can be achieved in manufacturing processes.
Challenges in Injection Molding
Despite its many benefits, injection molding is not without challenges. One significant issue lies in the initial cost of tooling and mold creation. Designing and producing a high-quality mold can require substantial upfront investment, which may deter smaller manufacturers without the capital to engage in such an expense. However, as technology advances and alternatives arise, these costs may gradually decrease, allowing wider access to injection molding capabilities. Furthermore, the production of complex designs can lead to issues such as warping and sink marks, requiring careful management during the cooling phase of the process. Manufacturers are tasked with not only creating the designs but also ensuring that they can be produced without common defects. Finding the right balance between complexity and manufacturability will continue to be a focus as designers push the envelope with innovative ideas.
Injection molding has undeniably transformed the landscape of modern manufacturing processes. With advantages such as cost-efficiency, design flexibility, and widespread applications across various industries, it remains pivotal in production strategies. Continuous technological innovations will only serve to enhance its role, with future advancements in materials and methodologies poised to refine the process even further. As the manufacturing industry continues to evolve, injection molding will remain a key player, driving efficiency and quality in production. With ongoing investments and collaborations, especially involving seasoned injection molding experts, the sector can look forward to overcoming challenges and embracing the opportunities that lie ahead.
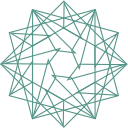
Citiesabc was created by a team of global industry leaders, academics and experts to create new solutions, resources, rankings and connections for the world’s top cities and populations.