Innovative Gear Technology: Enhancing Functionality Across Industries
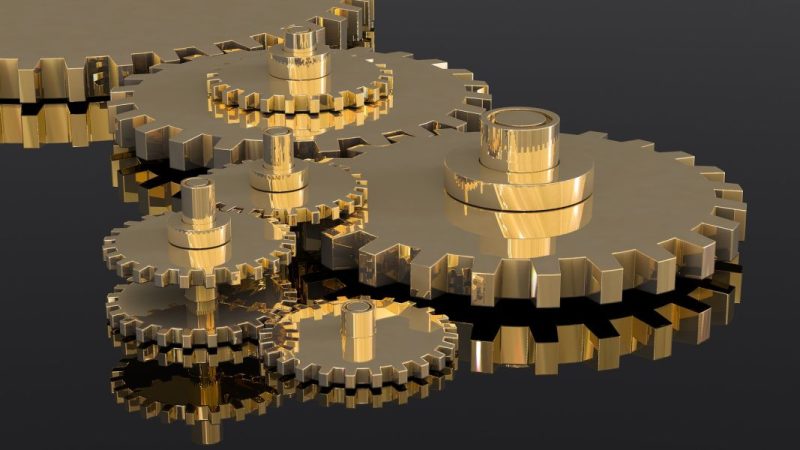
Categories :
Innovative gear technology has been a crucial component in enhancing functionality across various industries. From aerospace to healthcare, gear technology plays a critical role in improving efficiency, precision, and overall performance of machines and equipment.
Whether it's the gears used in aircraft engines or surgical robots, advancements in gear technology have revolutionized the way industries operate. The constant evolution of gear design, material selection, and manufacturing processes have allowed for the creation of more durable, efficient, and customizable gear systems.
In this blog post, we will discuss 8 ways innovative gear technology has enhanced functionality across industries. Without further ado, let's dive in.
Increased Efficiency
Innovative gear technology has significantly increased efficiency across industries by improving the transfer of energy and motion between machinery. Advanced gear systems, such as planetary gears and helical gears, reduce power loss and increase efficiency in comparison to traditional spur gears. This results in smoother operation, reduced heat generation, and ultimately lower energy consumption.
Moreover, advancements in gear design have allowed for the creation of more compact gear systems, reducing the overall size and weight of machinery. This not only improves efficiency but also makes equipment more portable and easier to operate. Innovative gear technology has played a significant role in increasing efficiency across industries, leading to cost savings and improved productivity.
Improved Precision
Innovative gear technology has also greatly improved precision in various industries. With the use of computer-aided design (CAD) software and advanced manufacturing techniques, gears can now be produced with high precision and tight tolerances.
This level of precision is crucial in critical applications such as aerospace and medical devices, where even the slightest error can have severe consequences. Also, as highlighted by the team behind Nabtesco Precision, innovative gear technology allows for the customization of gear designs to meet specific functional requirements. This ensures that gears are precisely tailored for their intended use, resulting in improved performance and reliability.
Enhanced Durability
Durability is a vital aspect of gear technology, especially in heavy-duty industrial applications. With the constant advancements in material selection and manufacturing processes, gears are now more durable than ever before. The use of high-strength materials such as hardened steel and specialized coatings has significantly increased the lifespan of gears, even under extreme operating conditions.
Moreover, innovative gear designs have also reduced wear and tear, leading to longer-lasting gear systems. For instance, the use of helical gears and involute tooth profiles distributes load more evenly, reducing stress on individual teeth and increasing overall durability. This has resulted in cost savings for companies as they can rely on durable gears that require less frequent replacement or maintenance.
Customizable Designs
One of the most significant benefits of innovative gear technology is the ability to customize gear designs according to specific functional requirements. This has allowed for the creation of unique gear systems that can perform specialized tasks in various industries.
For example, harmonic gears are widely used in robotics and automation due to their compact size and high precision, while hypoid gears are commonly used in automotive applications for their high torque capacity. The flexibility of innovative gear technology has opened up possibilities for tailored solutions, resulting in improved functionality and performance in different industries.
Reduced Noise and Vibration
In traditional gear systems, noise and vibration were often an issue, leading to discomfort for operators and potential damage to the equipment. However, with innovative gear technology, noise and vibration have been significantly reduced through advancements in design and material selection. Helical gears, for example, have helical teeth that reduce noise and vibration compared to straight-cut gears.
Additionally, the use of specialized lubricants and improved gear meshing techniques has resulted in quieter and smoother operation of gear systems, making them more comfortable for operators and extending the lifespan of equipment. This has been a crucial factor in improving functionality across industries, particularly in areas such as healthcare and transportation.
High Load Capacity
Innovative gear technology has also dramatically increased the load capacity of gear systems, allowing for heavier loads to be efficiently and safely transported. With the use of advanced materials and design techniques, gears can now handle higher torque and forces without failure or excessive wear.
This has opened up opportunities for industries such as mining, construction, and transportation, where heavy-duty equipment is necessary. For instance, in construction, heavy-duty gears are essential in cranes and earthmoving equipment, while the use of high-strength gears in truck transmissions has improved their hauling capacity.
The increased load capacity of gears has also resulted in more efficient and cost-effective designs, as fewer gears are needed to achieve the same output.
Increased Speed and Power Transmission
Innovative gear technology has also played a significant role in increasing speed and power transmission in various industries. With advancements in gear design and material selection, gears can now operate at higher speeds without compromising their efficiency or durability.
This has led to faster production processes, improved performance of vehicles and machinery, and increased power output in power transmission systems. A good example is the use of helical gears in wind turbines, which can operate at high speeds while efficiently converting wind energy into electricity.
The ability to transmit more power at higher speeds has also resulted in more compact gear designs, making equipment more efficient and versatile.
Compatibility with Advanced Control Systems
The integration of advanced control systems with innovative gear technology has further enhanced functionality across industries. With the use of sensors and computerized control, gear systems can now be continuously monitored and adjusted for optimal performance.
This level of precision and real-time monitoring allows for more efficient operation, reduced downtime, and improved safety. As industries continue to embrace automation and smart technology, the compatibility of innovative gear technology with advanced control systems will only become more crucial in enhancing functionality.
Innovative gear technology has greatly enhanced functionality across industries through its constant evolution in design, materials, and manufacturing processes. From increased efficiency and precision to customizable designs and high load capacity, gear technology has revolutionized the way machines and equipment operate. The compatibility of gear systems with advanced control systems has also opened up new possibilities for efficient and safe operation. As we continue to push the boundaries of technology, we can expect even more innovative gear solutions to emerge, further enhancing functionality across industries.
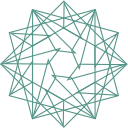
Citiesabc was created by a team of global industry leaders, academics and experts to create new solutions, resources, rankings and connections for the world’s top cities and populations.