Enhancing Workplace Safety with Proper Weighing Equipment

Categories :
Workplace safety remains a critical concern across various industries, particularly in environments that handle hazardous materials or operate under stringent regulatory standards. Among the diverse range of equipment essential for maintaining a safe working environment, weighing equipment plays a pivotal role.
This article explores how the right weighing solutions, like an explosion proof scale, can significantly enhance safety in industrial settings, contributing to a safer, more efficient operation.
The Significance of Weighing Equipment in Industrial Safety
Weighing systems are integral in numerous industrial processes, from manufacturing and pharmaceuticals to food production and chemical handling. The accuracy and reliability of these systems ensure that materials are processed correctly, preventing mishaps that might arise from incorrect measurements, such as overloading and underloading.
Preventing Overloads and Structural Failures
One of the primary roles of weighing equipment in enhancing workplace safety is preventing overloads. Industrial scales ensure that equipment such as silos, tanks, and lorries are not overloaded, which can lead to structural failures and significant safety hazards. Accurate weighing helps maintain the integrity of storage and transport vessels, safeguarding both the facility and personnel.
Enhancing Process Accuracy and Quality Control
Accurate weighing contributes directly to quality control by ensuring that the correct amounts of components are used in production processes. This precision is crucial in industries like pharmaceuticals and chemicals, where the safety and efficacy of products can be jeopardized by even minor deviations in ingredient quantities.
The Role of Calibration and Maintenance
The effectiveness of weighing equipment in promoting safety is contingent upon regular maintenance and calibration. Calibration ensures that weighing systems provide consistent, accurate results, while regular maintenance prevents malfunctions that could lead to accidents.
Routine Checks and Balancing
Routine checks and calibrations minimize the risk of errors that could otherwise lead to hazardous situations. For example, in chemical manufacturing, an uncalibrated scale might lead to an incorrect mixture of reactive substances, potentially resulting in dangerous reactions.
Software Integration and Automation
Modern weighing systems integrated with software provide automated alerts when maintenance is due, or anomalies are detected. This integration enhances safety by addressing potential issues proactively before they can lead to serious safety incidents.
Specialized Equipment for Hazardous Environments
In environments where flammable gasses, dust, or chemicals are present, the risk of explosions is a significant concern. Explosion-proof scales are designed specifically for such settings and are equipped with features that prevent the ignition of surrounding volatile substances.
Design and Functionality
Explosion-proof scales are constructed with materials and components that contain and isolate sparks or heat that could trigger an explosion. The design considerations also extend to the operation interface and power supply, ensuring all aspects of the scale contribute to a safer work environment.
Regulatory Compliance
Using an explosion proof scale not only enhances safety but also ensures compliance with various safety regulations and standards. Facilities implementing these specialized scales demonstrate a commitment to safety and regulatory adherence, which is crucial for operational licensure and reputation.
The Impact of Advanced Weighing Technology on Safety
Advancements in weighing technology continue to refine the safety benefits of these systems. With the advent of IoT and intelligent technologies, weighing equipment can now communicate with other systems within a facility, leading to integrated safety measures that are proactive rather than reactive.
Real-Time Monitoring and Data Analysis:
Integration with Facility Systems: Beyond just detecting weight inconsistencies, smart scales can communicate with other systems in a facility, such as inventory management or production control. For instance, if a shipment exceeds a specific weight limit, the system can automatically alert relevant personnel or adjust production schedules accordingly.
Historical Data Analysis: These systems not only monitor current weights but also collect historical data for analysis. By analyzing trends over time, patterns of inefficiencies or potential safety hazards can be identified and addressed proactively.
Customizable Alerts and Notifications: Users can customize alert thresholds based on specific safety requirements or regulatory standards. This flexibility ensures that personnel are alerted promptly to any deviations from normal operating conditions, allowing for swift corrective action.
Predictive Maintenance and Alerts:
Condition-Based Maintenance: Advanced weighing technology can utilize data analytics and machine learning algorithms to predict when maintenance will likely be required based on equipment usage patterns, environmental conditions, and performance metrics. This shift from traditional time-based maintenance schedules to condition-based maintenance can optimize equipment uptime and longevity.
Remote Monitoring and Diagnostics: IoT-enabled weighing systems allow for remote monitoring and diagnostics, enabling maintenance teams to identify potential issues without physically inspecting the equipment. This capability reduces downtime by facilitating rapid troubleshooting and targeted maintenance interventions.
Automatic Work Order Generation: When a potential maintenance issue is detected, smart scales can automatically generate work orders or service requests, streamlining the maintenance process. This automation ensures that maintenance tasks are prioritized and assigned promptly, minimizing the risk of prolonged equipment downtime.
The integration of proper weighing equipment is not just a necessity for operational accuracy but a cornerstone of industrial safety. By choosing suitable scales, maintaining them correctly, and utilizing advanced technologies, industries can safeguard their workforce and premises from potential hazards. The investment in high-quality, suitable weighing equipment, including explosion-proof scales for hazardous environments, pays dividends not only in compliance and efficiency but fundamentally in safety. This proactive approach to workplace safety through advanced weighing technology fosters a culture of safety that permeates every level of operation, ensuring that safety is not just observed but integrated into the very fabric of industrial processes.
Read More:
bill gates smart city in arizona
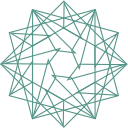
Citiesabc was created by a team of global industry leaders, academics and experts to create new solutions, resources, rankings and connections for the world’s top cities and populations.